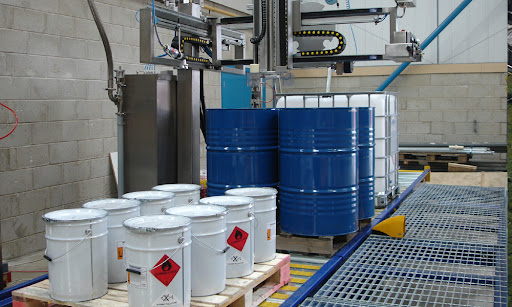
A Carboy drum filling machine represents the pinnacle of precision liquid handling technology in today’s rapidly evolving industrial landscape. These remarkable systems have transformed how businesses manage their liquid transfer operations, bringing unprecedented levels of efficiency, accuracy, and safety to manufacturing processes worldwide.
The Evolution of Liquid Filling Technology
The journey from manual filling methods to automated solutions has been nothing short of revolutionary. Traditional approaches to filling carboys and drums were labour-intensive, time-consuming, and prone to human error. Workers would physically manoeuvre heavy containers, manually operate valves, and visually estimate fill levels—a process that was not only inefficient but potentially hazardous.
Fast forward to today, and the contrast couldn’t be more striking. Modern carboy drum filling machines employ cutting-edge technology to deliver:
· Precise volumetric measurements down to millilitres
· Automated start/stop functions eliminating overflow risks
· Programmable fill parameters for different container sizes
· Real-time monitoring and data logging capabilities
· Explosion-proof options for hazardous environments
“The best filling machinery doesn’t just transfer liquid—it transforms your entire operation through radical efficiency gains that compound over time.”
Game-Changing Benefits for Forward-Thinking Operations
Let’s be absolutely clear: implementing advanced filling technology isn’t just an upgrade—it’s a complete paradigm shift for any operation handling liquids at scale.
Unmatched Precision and Consistency
With programmable controls and advanced flow meters, these machines deliver fill accuracy typically within ±0.5%, dramatically reducing product wastage and ensuring consistent quality across your entire production run. This level of precision was simply unimaginable with manual methods.
Exponential Productivity Gains
The mathematics here is straightforward but profound. A well-designed carboy filling system can often achieve filling rates 5-10 times faster than manual methods while requiring fewer personnel. One Singapore-based chemical manufacturer reported a 73% reduction in filling time after implementing an automated solution.
“When you’re scaling production, the difference between manual and automated filling isn’t incremental—it’s exponential. What took hours now takes minutes.”
Dramatically Enhanced Safety Protocols
The statistics on workplace injuries related to manual drum handling are sobering. Automated filling systems eliminate many of these risks through:
· Reduced physical handling of heavy containers
· Enclosed filling operations minimising exposure to hazardous substances
· Emergency shutdown systems that activate instantly when abnormalities are detected
· Customised safeguards for specific chemical compatibility requirements
Selecting the Right System: Critical Considerations
The optimal filling solution must be tailored to your specific operational requirements. When evaluating options, consider these vital factors:
Throughput Requirements
Calculate your desired containers per hour and ensure the system can meet or exceed this rate with room for future scaling. Always factor in your growth trajectory—the goal is to invest in technology that grows with you, not one you’ll outgrow quickly.
Liquid Properties
Different fluids demand different filling technologies. Viscous liquids may require positive displacement pumps, while corrosive chemicals need compatible materials throughout the fluid path. Temperature sensitivity, foaming tendencies, and specific gravity all influence the ideal configuration.
Integration Capabilities
The most powerful systems don’t operate in isolation—they communicate with your broader manufacturing ecosystem. Look for machines with modern connectivity options that can integrate with:
· Inventory management systems
· Quality control databases
· Production scheduling software
· Regulatory compliance tracking tools
Environmental Impact: The Hidden ROI
Going beyond operational efficiency, modern filling systems deliver substantial environmental benefits that forward-thinking operations cannot afford to ignore. Precise volumetric control dramatically reduces product wastage—an advantage that translates directly to reduced environmental footprint. When handling chemicals or hazardous materials, this precision means less waste requiring specialized disposal procedures and reduced risk of environmental contamination.
“The most sustainable manufacturing is the kind that wastes nothing. Precision filling technology isn’t just good business—it’s responsible stewardship of resources.”
Customization: Beyond One-Size-Fits-All Solutions
The industrial market increasingly demands tailored solutions rather than off-the-shelf products. Leading manufacturers now offer customizable filling systems that can be precisely configured to specific operational needs:
· Multi-head filling stations for parallel processing
· Clean-in-place (CIP) systems for pharmaceutical or food-grade applications
· Weight-based verification systems working in tandem with volumetric filling
· Nitrogen purging capabilities for oxygen-sensitive products
· RFID tagging integration for complete batch traceability
ROI: The Numbers That Matter
Investing in automation always raises questions about return on investment. The economics of automated filling systems present a compelling case:
· Labour costs typically reduced by 40-60%
· Product loss from overfilling reduced by up to 95%
· Production throughput increases of 200-500%
· Maintenance downtime reduction of approximately 30%
The Future is Automated
As manufacturing continues its inexorable march toward complete automation, the humble filling operation stands at a critical crossroads. Forward-thinking operations are recognizing that liquid handling represents not just a necessary process but an opportunity for significant competitive advantage.
The industrial landscape is transforming at breathtaking speed, and those who fail to upgrade critical infrastructure will inevitably fall behind. Whether you’re handling chemicals, food products, pharmaceuticals, or any other liquid commodities, the message is clear: automation isn’t just coming—it’s already here, and its impact is profound. For operations serious about maximizing efficiency while minimizing risk and waste, there’s simply no substitute for investing in a high-quality Carboy drum filling machine.